Overview
CoolPlanet and their in house energy optimisation platform, CoolPlanetOS, were tasked with decreasing electrical & fuel consumption within a feedmill plant, without negatively affecting production.
Key Stats
€313,315
Electrical Savings
€180,503
Fuel Cost Savings
€493,818
Total Savings
Electrical Savings
Cooling
The majority of electrical consumption in feed mills comes from motors. The motors can be split up into two categories, one category covers motors that have an application that requires constant speed, the other category covers motors that can be ramped up or down depending on the process requirements.
CoolPlanetOS, our in house energy optimisation platform along with our engineering team, identified each target motor and the most efficient and feasible solution that could be applied to them.
Motors that require constant speed and that have variable loads can be optimised by installing a fixed speed motor controller (FSMC). In common with all soft start devices FSMCs use thyristors to accurately control the voltage applied at the motor terminals. A characteristic of the Thyristor to switch rapidly from “OFF” to “ON” when pulsed, and to remain “ON” until the current through the device falls to zero at the end of each half-cycle in the AC supply, is called self-commutation.
When working at or near full load, the typical 3-phase induction motor is relatively efficient, achieving efficiencies of between 80% to 92%. However, motor efficiency falls dramatically when the load falls to less than 50% of rated output. In fact, very few motors actually experience consistent fully rated operation, the vast majority operate at much lower loads due to either over-sizing (a very frequent situation), or natural load variations. In applications where motor speeds do not need to be varied, the optimisation software in the Integra will produce energy savings in lightly loaded motors.
Less sophisticated soft-starters remain at full conduction and the motor then behaves as if it were connected directly to the mains supply. However, at light loads at full mains voltages, induction motors always have excess magnetising current. By detecting the load at any instant, and adjusting the motor terminal voltage accordingly, Integra is able to save some of the excitation energy and load loss, and improve motor Power Factor when the motor is running inefficiently at light loads. Circa 32 FSMCs were installed on each site, motor ratings ranging in size from 11kW - 315kW.
VSDs (variable speed drive) can be installed on motors that are in use on applications where the motor speed can vary and be controlled depending on what the process requires. Feed mills use equipment called pelleting presses. This equipment comprises two motors that drive the same shaft via belts. Without VSDs these motors cannot run at the exact same speed, one motor will work harder than the other. This technique of driving the shaft is inefficient, with VSDs installed on both motors, the VSDs can communicate to each other and the PLC and run in tandem, so they share the load equally. This leads to a much more efficient process.
The pelleting process is required to pellet raw materials that are made up with different recipes. Different recipes can be pelletized by the presses at different motor speeds without compromising quality. Each recipe was assigned as low a speed as possible allowing the motors to consume just the right amount of power required.
Circa 32 VSDs were installed on each site ranging in size from 55kW-160kW.
VSDs were also installed on cyclone fans, these fans extract heat from a chamber (cooler) filled hot heated pellets from the process. These pellets need to be cooled sufficiently so as not to compromise their physical integrity. The cooler fans were running at a 100% before the project but with the installation of temperature probes in the coolers and pressure transmitters in the ducting from the fans to the coolers an optimum temperature can be obtained by controlling the speed of the fans in a control loop and again the optimum amount of power is used by the fans.
There was also a new variable speed air compressor installed which replaced a fixed speed air compressor. The VSD allowed for the compressor to ramp up or down depending on the air used onsite. This air compressor was also installed with a heat recovery system. Circa 90% of an air compressors consumed energy is wasted via heat.
This heat was recovered and used to preheat the feed water that topped up a hotwell. So instead of 10 degree mains water topping up the hotwell, 40 degree water was instead topping it. This allows for less steam to be used from the boiler to keep the hotwell at an optimum temperature of 85 degrees.
Lighting
All fluorescent lighting onsite was also replaced by commercial LED lighting.
Thermal Savings
Prior to the CoolPlanets project, there were 2 boilers onsite, one fed from natural gas and another from light fuel oil, both in operation in excess of 15 years. Both boilers were highly inefficient. Increasing the efficiency of the steam system on both sites was targeted in a number of ways and was identified by CoolPlanetOS.
Insulation upgrades were carried out across the entire steam network. This consisted of piping insulation and valve insulation. This measure decreased the amount of energy that was radiated out from uninsulated pipes and valves. All mechanical steam traps onsite were swapped out for venturi type steam traps. Mechanical steam traps operate with moving parts which are prone to failing. These traps can fail open, which in essence is like a constant steam leak or failed close which negatively impacts the process. Venturi type steam traps have no moving parts and allow condensate to exit the live steam system much more efficiently.
The control on one steam boiler was optimised, this consisted of a much tighter control around its SP pressure and the installation of a new TDS blowdown control system was also utilised. The other steam boiler was replaced by a new efficient boiler; a gas fired steam boiler. The boiler house was also revamped during the project. A new softener set and RO was installed to ensure properly treated water was feeding the newly installed boiler. They help prevent any build up of particulates in the boiler which would lead to scaling and lower the running efficiency.
The main steam lines off the header were also fitted with Y strainers to contribute to cleaning out the steam system onsite The boiler was also equipped with an oxygen trim system which analyses the oxygen content in the hot gases exiting via the boiler flue and dependant on the %, it will control the amount of air that is introduced into the burner so ideal combustion can occur. The boiler was also installed with an economiser which preheats the water topping up the boiler.
Project Complete
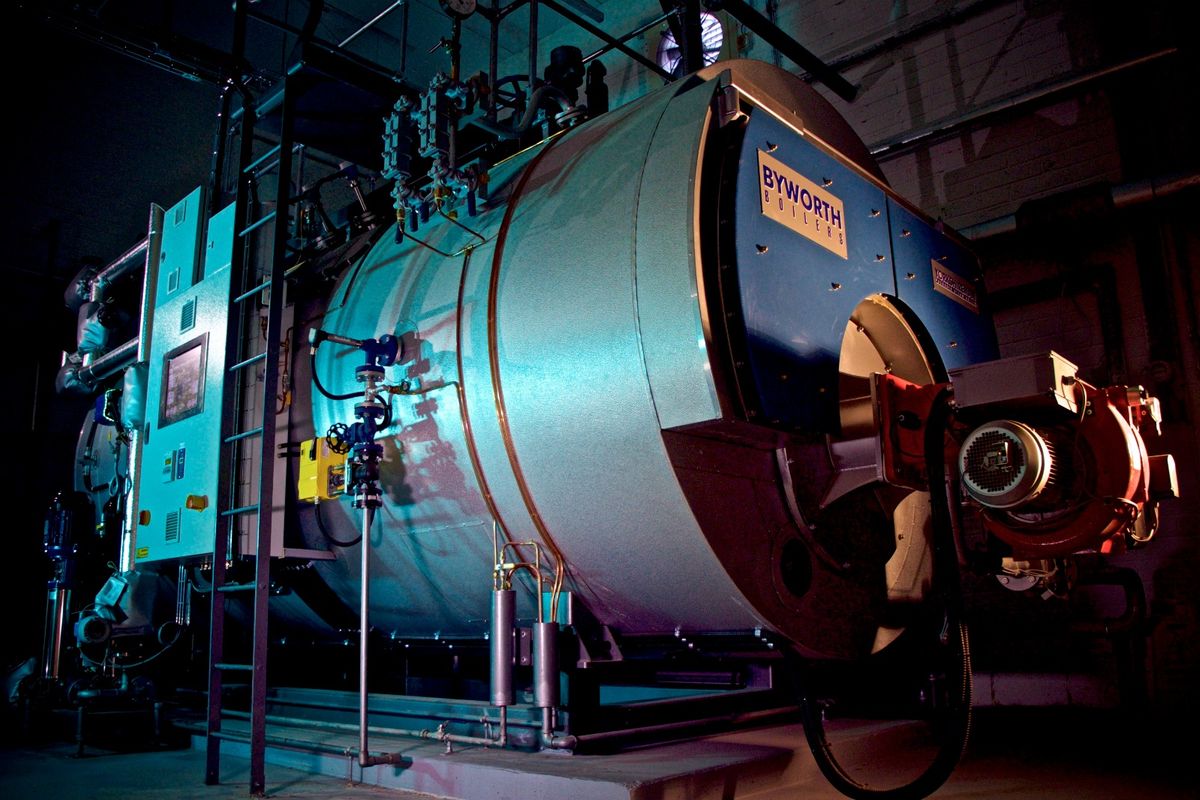
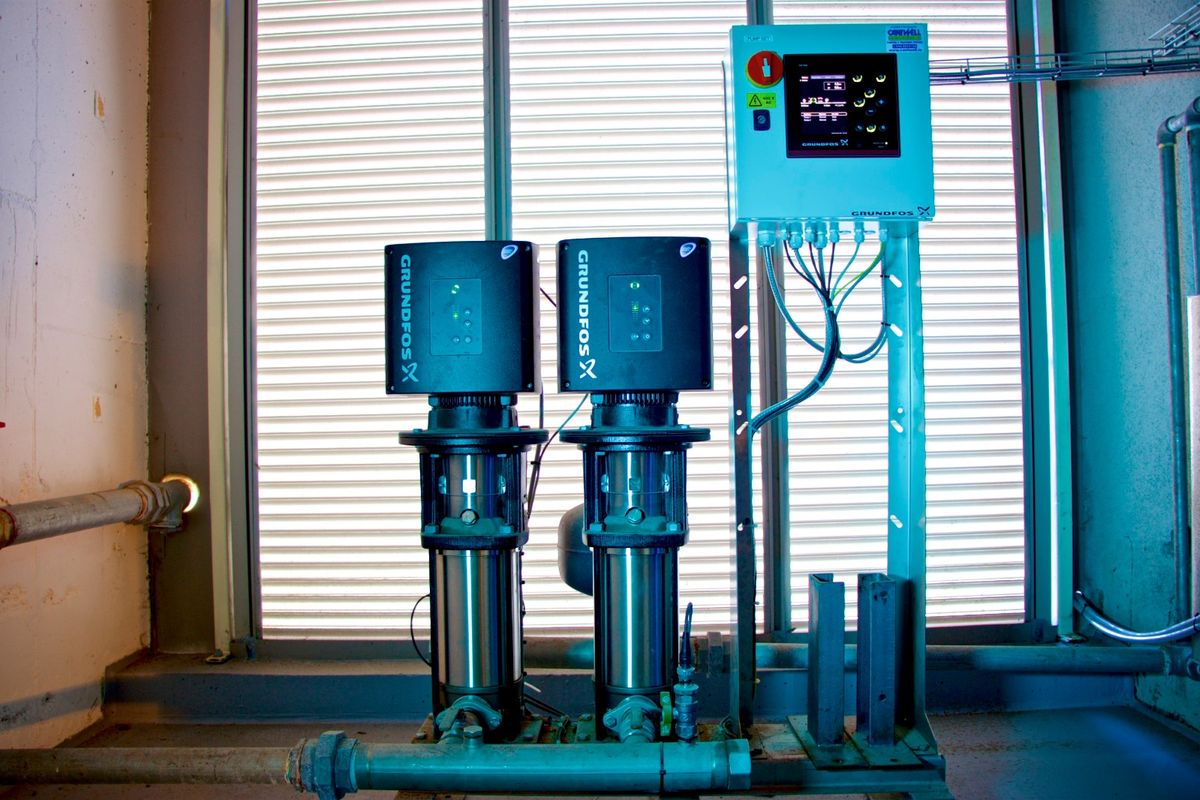