Overview
A global agribusiness company with nearly 100 production sites has been investing in a program to improve energy efficiencies on their sites. To investigate significant energy consumption and associated opportunities, a handful of sites were selected for energy audits and upgrades across multiple continents. Two of these were in Brazil, including a soybean crush facility for edible oils.
The facility is one of the largest of its kind in the world and its four biomass boilers have a combined output of 105 metric tons per hour. Three different types of fuel are burned, amounting to an annual total fuel cost of R$18 million (US$3.24) and an average steam cost of R$46 (US$7.3) per metric ton – this was before optimization of the system.
Key Stats
R$4.3Million/Year
Fuel Cost Savings
R$6 Metric Ton
Average Steam Cost Savings
2 Years
CAPEX Payback
The annual fuel usage is:
- Brachiaria (strawbale): 23,500 tons/ year
- Whole logs: 25,500 tons/ year
- Woodchips: 62,500 tons/ year
Challenges
Identifying the Challenges
Global energy services company CoolPlanet came on board in 2018 to do an onsite Investment Grade Audit (IGA) and identify savings opportunities. CoolPlanet has a global track record in reducing the energy consumption and spend of large industrial companies by combining leading-edge engineering, financing and technology solutions with a passion to build long-term sustainable planet-positive solutions to reduce the world’s production of carbon emissions.
An initial period of system assessment and baselining followed, where the CoolPlanet team worked very closely with the client to coordinate and collaborate on the best possible energy efficiency improvements given the available budget and targets. Project implementation commenced from March to December 2019 with testing and snagging continuing into 2020.
The IGA was key to identify potential opportunities and savings. It was important to not only understand the equipment on site, but how it was being operated.
By collecting historical data as well as going to site and doing in-depth testing and measurement, as well as interacting with the biomass boiler operators and maintainers, CoolPlanet was able to identify various operational challenges and ways to optimize the overall system operation.
Challenges Found
When starting this process, it was immediately clear that very little data was being collected from the biomass boilers. None of the biomass boilers had oxygen analyzers that worked and there was no feedback on the efficiency of the combustion process. To determine the baseline performance, the CoolPlanet team used biomass flue gas analyzers to test a variety of indicators such as carbon monoxide, nitrogen, nitrogen oxides, sulfur oxides, flue gas moisture, temperature, etc.
Classifying the fuel was a critical task and it was clear that the site did not have a fuel sampling/ testing program in place. As such, multiple samples of fuel and ash, off each boiler, were taken and sent off for professional analysis by CoolPlanet. The analysis included a variety of things, including ultimate and proximate analyses of the fuels and, for the ash samples, an elemental analysis, fusion temperatures and a sieve analysis to validate the particle size. This was all key to understanding how the system is operating and how it could operate with modifications.
The condensate return was about 35-40%, which meant that a large amount of steam ended up as wastewater. With so much water to make up for, an important element of the project was to recover as much waste heat as possible into the make-up water to reduce the load on the boilers, thus the fuel burned. The boiler capacity was also found to be oversized, in number of biomass boilers as well as total installed capacity. Despite having a 105-ton/ hour capacity, CoolPlanet found that the operation only required a maximum of 60, which led to great inefficiencies in operation of each boiler as well as total cost to own and operate.
Another obvious challenge was the fact that the boilers had multiple fuel sources, which weren’t optimally managed when fed into the boilers. This, in addition to not having adequate process data on hand to make better operating decisions, had a destabilizing effect on the pressures in the boilers.
The control systems were also found to be substandard, as well as the level of data collected and used by the operators. Unfortunately, on this site (like so many others), there was limited data available on the combustion of the fuel. Only the fuel arriving on site was measured, nothing else – which importantly included the moisture content of the fuel.
Operational decisions that should have been made to account for fuel quality were missed without information related to the quality of fuel available.
The Solution
The total annual fuel cost was R$18 million (US$3.24) previously but thanks to the modifications made by CoolPlanet, this cost came down to R$13.7 million (US$2.47 million), achieving an annual saving of R$4.3 million (US$770,000).
The CoolPlanet team was led by Jason Garner in the U.S., who boasts more than 16 years of specialized experience in working (which includes combustion system and boiler design, installation, commissioning, and operation) with biomass energy boilers.
For this project, Garner and his team opted for low impact changes that resulted in the most benefit. Importantly, the modifications didn’t require the shutting down of the plant; it could be implemented with little disturbance to operations. With the help of CoolPlanetOS, CoolPlanet focused on improving the envelope of each boiler, resulting in a more efficient boiler. Built with the company’s deep engineering experience in retrofitting manufacturing and industrial process sites, CoolPlanetOS offers the industry’s first Software as a service (SaaS)-based solution for real-time monitoring and analysis of energy consumption, providing insights into which machinery, process, product line, or site is currently not performing as expected.
Data is only one part – the other is action. As such, the CoolPlanet team took all the data they gathered, consolidated it with other operating parameters and turned this into actionable improvements. One of these improvements was modifying the way fuel was fed on two of the boilers, minimizing the oxygen being pulled in from the door being opened and thus managing the steam pressure. The goal was to reduce variability of the pressure in the system. This improvement also greatly reduced a safety hazard where the operators, who stand at the boiler to feed fuel, are no longer exposed to the radiant heat from the furnace when the fuel door is opened.
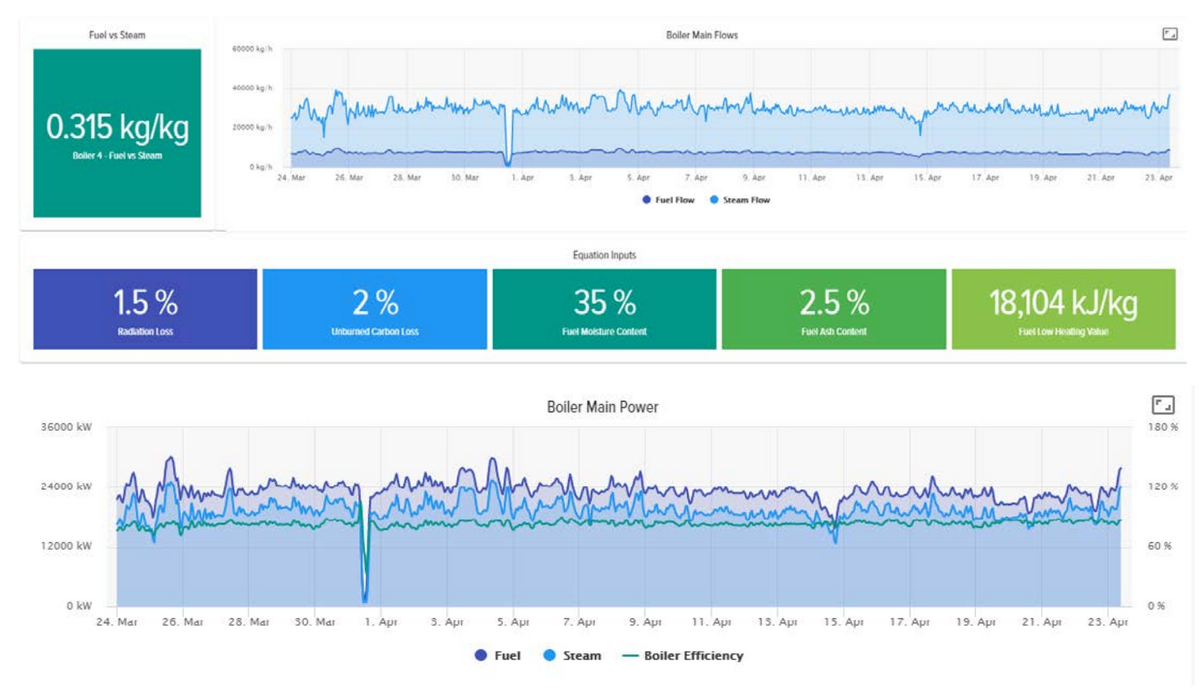
CoolPlanet also implemented a brand-new cascade-type control system that allows Boiler 4 to be fully automated and turned down when capacity isn’t needed. This control system is also more user-friendly and allows Boiler 4 to function completely automatically, with the exception of adjusting boiler pressure and oxygen setpoints. This frees up staff to focus on the more manual, labor-intensive tasks associated with feeding the remaining three biomass boilers. Master boiler controls were also designed and implemented on Boilers 1, 2, and 3. The master controls allow for semi-automatic operation of these boilers, which were almost completely manual before the modifications.
In addition to all of the new modifications at each boiler, CoolPlanet put in a new fuel feed control panel at two of the manually fed boilers. This empowers operators with better information to rate the quality of their decisions so they can modify their behavior and improve efficiency and reduce the erratic nature of the system steam pressures. A variety of heat recovery improvements were also made, including blowdown on the biomass boilers to recover wasted energy into makeup water and flash steam directly into each deaerator to reduce live steam required for deaeration. A new air heater was also installed to dry soybeans with hot air as well as a new economizer on the oldest boiler. Heating with hot air is more efficient than heating with steam and by using the clean hot air (instead of the boiler’s chimney gas), there is no risk of developing carcinogens in the product and it allows the plant to sell their product to more customers.
Results
By improving the operations of the plant, it also improved the performance of the facility. Thanks to the modifications made and new data being provided, the lives of the operators are easier. By empowering the operators to make more informed decisions, it is better for the environment as well because emissions are being lowered by way of better combustion of the fuel required as well as lowering the total fuel input required by way of more efficient operations and better utilization of the steam in the process.
The total annual fuel cost was R$18 million (US$3.24) previously but thanks to the modifications made by CoolPlanet, this cost came down to R$13.7 million (US$2.47 million), achieving an annual saving of R$4.3 million (US$770,000).
The average steam cost also improved. Previously, this cost was estimated at R$46 (US$7.63) per metric ton, a number that was improved to R$40 (US$6.63) tons, saving R$6 (US$1) per metric ton. In terms of capital expenditure (CAPEX), the payback of the improvements made by CoolPlanet is estimated at only two years.